The Manufacturing
Process of Lead Crystal
We have some video coverage of the the
manufacturing process which also has some excellent pictures of the
crystal.
The
manufacturing of glass is an art and process
established over 2000 years ago and uniquely
has changed very little apart from the
addition of lead to create today's lead
crystal. Lead crystal usually comprises of
48% silica sand, 24% potash and 28% red
lead.
The lead
crystal formula is mixed and turning into
molten crystal in a furnace heated over
2000F. Red lead is added into the furnace to
create the purity and density.
Lead crystal
is blown glass but because of its weight and
thickness it requires a coordinated team of
blowers. They use their skill and experience
to create the glass body to the correct
thickness. This is necessary to enable the
glass designs to be deep cut. At this time
other parts such as handles can be added.
The pieces are
then placed in an annealing oven - under
controlled conditions the oven slowly and
evenly heats the glass to an annealing
temperature. After a brief soaking period to
ensure even heat distribution throughout the
glassware, the oven temperature is slowly
returned to room temperature.
The lead
crystal glass is now ready to be cut. A
pattern is drawn on the items and then
mapped out with a power wheel. The finished
design is then completed using diamond tip
wheels using a combination of flat and wedge
cuts to provide contrast, followed by the
smoothing process on a sandstone wheel.
To finish the items it is
dipped into a combination of sulphuric and hydrofluoric acid
which removes a thin layer of glass providing a uniform and
lustre finsih.
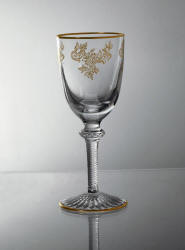
Adagio by Montbronn of France
If engraving is required or
is part of the pattern small copper wheels are used which
required great skill, patience and care
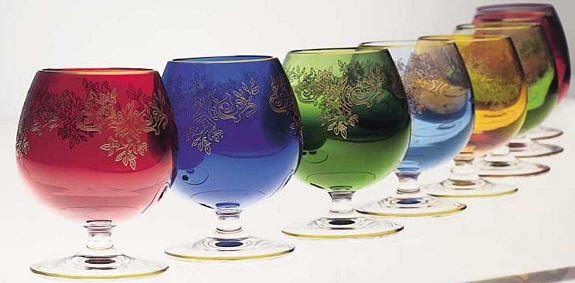
Adagio Cased Crystal by
Montbronn of France |